Cargo damage, shipment damage, transit damage—no matter what you call it, 4over is committed to minimizing it in every way possible. For the past several months, the 4over Logistics and Operations teams have been working hard to reduce product damage during shipping, delivery, and handling. While preventing damage during transit is an ongoing priority, with the surge in shipping since the pandemic, we have noticed an increase in issues such as damaged boxes. This put the two teams’ effort into an even higher gear. They’ve been experimenting with a number of variables, from using different size configurations and trying different taping methods to using certain weight and strength combinations.
Our Expert Testing Partner in Preventing Product Damage
Our logistics team wanted scientific analysis to back up their observations and feedback from our customers about these issues, so they reached out to the experts at Advance Packaging Technology Laboratories for additional help. It’s not an exaggeration to say that the gamut of tests 4over had performed on our shipping boxes make the obstacle course on American Ninja Warrior look easy.
How Our Product Packaging Was Tested Using ISTA Standards (aka Package Ninja Warrior)
Now we’re getting into the tough stuff (literally). 4over’s product packaging testing was conducted according to the International Safe Transit Association (ISTA) test procedures and standards, which are developed according to package type and size. The testing process described here is for Project 3A Standard, Packaged Products for Parcel Delivery Shipment 70kg (150lbs) or less, for Flat Packages.
Our version of ninja contestants—aka our test packages—were subjected to two drop sequences as well as random vibration testing.
- Falling Objects Ahead: In the first round of drop testing, the package was dropped nine different times from a height of 18 inches onto different edges.
- Shake It Up: Next, packages were placed on a vibration table and a top load added. Using a pattern that mimics over-the-road transport, the package was subjected to 150 minutes of vibration, divided between three face orientations of the package.
- Ouch: The second drop sequence included eight additional drops on a variety of edges, again from a height of 18 inches.
- Hanging Tough: Finally, the packages were subjected to rotational edge drops of 8 inches, rotational flat drops equal to the package height and a concentrated impact test in which a 9lb hazard box is dropped from a height of 16 inches directly onto the center of the packages being tested.
Whew! By the way, the requirement for our package ninja warriors to “pass” the test was no visible damage, with the product intact and the packaging components able to provide further protection.
4over Scores a Victory Over Transit Damage
We are proud to say that our packaging in this test rang the bell—enduring the abuse to meet the ISTA 3A Flat Acceptance Criteria. In accordance with Advance Lab’s expert recommendations, we are also making changings to shipping for some products.
- Replacing our B9 boxes, primarily used for shipping booklets and brochures, with 275-lb Mullen boxes that provide a higher burst tolerance.
- Testing new packing methodologies for our grand format products that will add more support to the corners of those boxes.
And to help prevent shipping damage of any kind during transportation, 4over is extending our commitment to rolling out this type of intensive testing and implementing recommended improvements across our entire product line.
Packaging to Prevent Damage: A Better Way to Tape Boxes
One instant improvement that our experts were able to help us implement was a new method for taping packages. Called a “H Style Taping”, this 8-step process is specifically designed to be efficient while providing a solid seal and strong support. It also has the added benefit of being tamper-resistant, because the amount of tape that must be removed to open the box makes tampering efforts difficult and obvious. We’ve already begun applying this new taping standard to our G4M shipping, with plans to expand the practice across all shipped items over time.
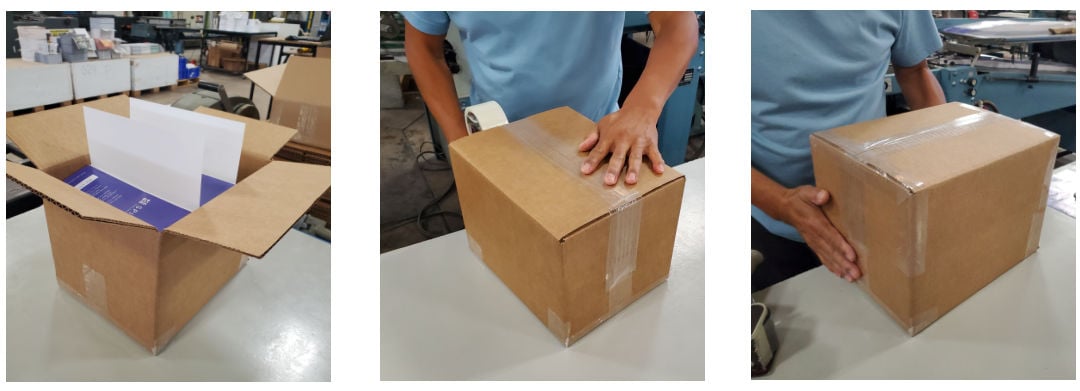
TAPPI Standards Also Prevent Product Damage
4over also invested in standalone testing of our shipping containers (as opposed to the complete packaging process) using established TAPPI standards (TAPPI stands for the Technical Association of the Pulp and Paper Industry). These tests were conducted to confirm that the packaging materials meet the technical standards claimed by the manufacturers normally stamped on each packaging material. As a result of that initiative, we will be carefully monitoring the quality of the packaging our vendors deliver to ensure that it is consistently up to standards for both resistance to edge crushing and appropriate bursting strength.
If you’d like to know more about our efforts to protect your goods during transportation, one of our Customer Service Specialists would be happy to help. You can reach us at 1-877-782-2737 Monday - Friday, 6AM-4PM Pacific Time, or email any time!